- Evaluate manufacturing processes; applying knowledge of product design, fabrication, assembly, tooling, and materials; conferring with equipment vendors; soliciting observations from operators.
- Develops manufacturing processes by studying product requirements; researching, designing, modifying, and testing manufacturing methods and equipment; conferring with equipment vendors.
- Improves manufacturing efficiency by collecting data and working with more senior manufacturing engineers to analyze and plan staffing, work flow, space requirements, and equipment layout.
- Assures product and process quality by designing basic to intermediate complexity testing methods; testing finished- product and process capabilities; establishing standards; confirming manufacturing processes.
- Provides manufacturing decision-making information to management by calculating production, labor, and material costs; reviewing production schedules; estimating future requirements.
- Prepares product and process reports by collecting, analyzing, and summarizing information and trends.
- Possesses a basic level of understanding or background in lean manufacturing, fixture design, part design, design for manufacturing and assembly practices.
- Creates and maintains manufacturing records including Bills of Material, assembly and test procedures and work instructions, and test records.
- Implements continuous product improvements aimed at improving reliability, design for manufacturability and assembly (DFMA), as dictated by customer needs and requests.
- Keeps production and test equipment operational by coordinating maintenance and repair services; following manufacturer's instructions and established procedures; requesting special service.
- Maintains professional and technical knowledge by attending educational workshops; reviewing professional publications; establishing personal networks; participating in professional societies.
- Support floor personnel in assembly for manufacture, troubleshooting documentation and design issues to resolution.
- Support Program/Project Managers by providing technical assistance
- Perform costing and /or estimates for product changes or new products.
- Direct activities and provide guidance and oversight to manufacturing technicians.
- Bachelor of Science in Engineering.
- 0-6 years’ experience working in an ISO regulated capital equipment product manufacturing environment.
- Working experience with CAD (SolidWorks preferred), MS Office, MS Project, and MRP/ERP systems.
- Good technical aptitude and basic understanding of electro/mechanical assemblies.
- May have basic knowledge of MRP/PDM; Epicor E9/10 and SW EPDM software experience a plus.
- Basic knowledge of GT&D, inspection methods and tools.
- Generally works in an office environment, but may occasionally be required to perform job duties outside of the typical office setting. Occasional travel required.
- Interaction with people and technology while either standing or sitting.
- Must be able to communicate face-to-face and on the phone.
- Able to lift up to 50 lbs.
Columbia Tech is an Equal Opportunity Employer. Columbia Tech does not discriminate on the basis of race, religion, color, sex, gender identity, sexual orientation, age, non-disqualifying physical or mental disability, national origin, veteran status or any other basis covered by appropriate law. All employment is decided on the basis of qualifications, merit, and business need.
We are an equal opportunity employer and all qualified applicants will receive consideration for employment without regard to race, color, religion, sex, national origin, disability status, protected veteran status, or any other characteristic protected by law.
Columbia Tech provides world-class product development, manufacturing, global fulfillment, and aftermarket services to a diversified group of capital equipment innovators in the medical, life sciences, energy, homeland security, robotics and automation, communications, 3-D printing, semiconductor, LED, water treatment, and food and beverage industries.
OUR MISSION AND VISION
Coghlin Companies is a fourth generation, privately held Time to Market Services company providing world-class product development, manufacturing, global fulfillment, and aftermarket services to a diversified group of capital equipment innovators in the medical, life sciences, energy, homeland security, robotics and automation, communications, 3-D Printing, semiconductor, LED, water treatment, and food and beverage industries.
Through our proprietary Scaled Product Launch (SPL™) process, we commercialize complex capital equipment products at WARP SPEED with great quality, compliance, competency, passion, and transparency. We leverage lean manufacturing and our global supply chain network to continuously reduce the cost of client products and deliver them to the marketplace quicker than the competition.
For more than 130 years, our passionate team of Caring Associates has remained focused on creating positive first impressions and exceptional customer experiences with clients by promoting a culture of collaboration and long-term trustful relationships, enabling a higher probability of product launch success and unmatched referability.
(if you already have a resume on Indeed)
Or apply here.
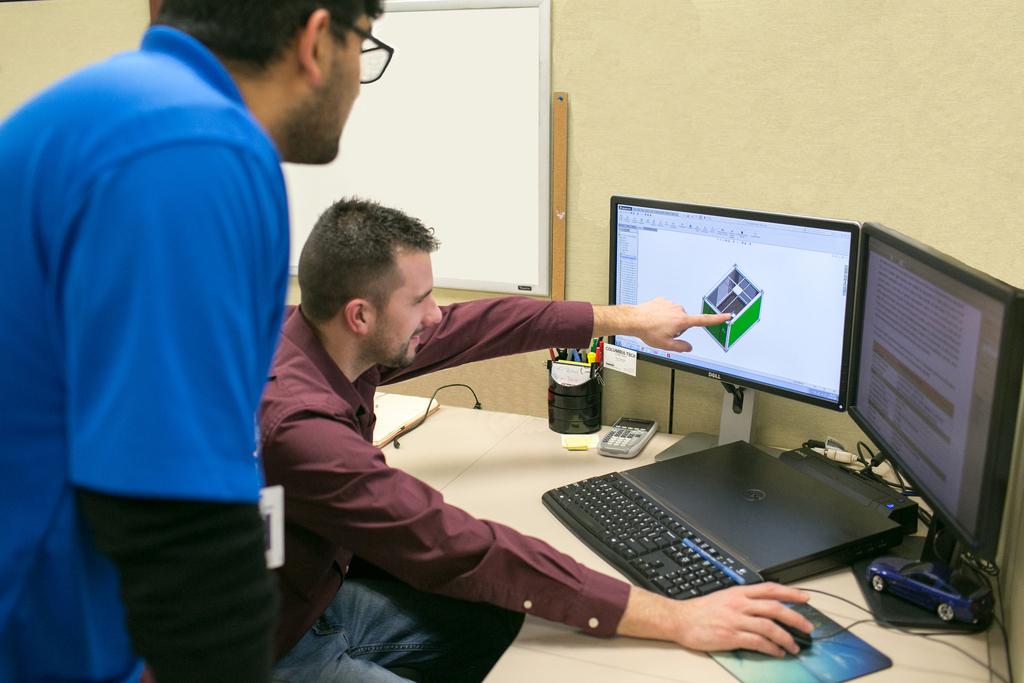
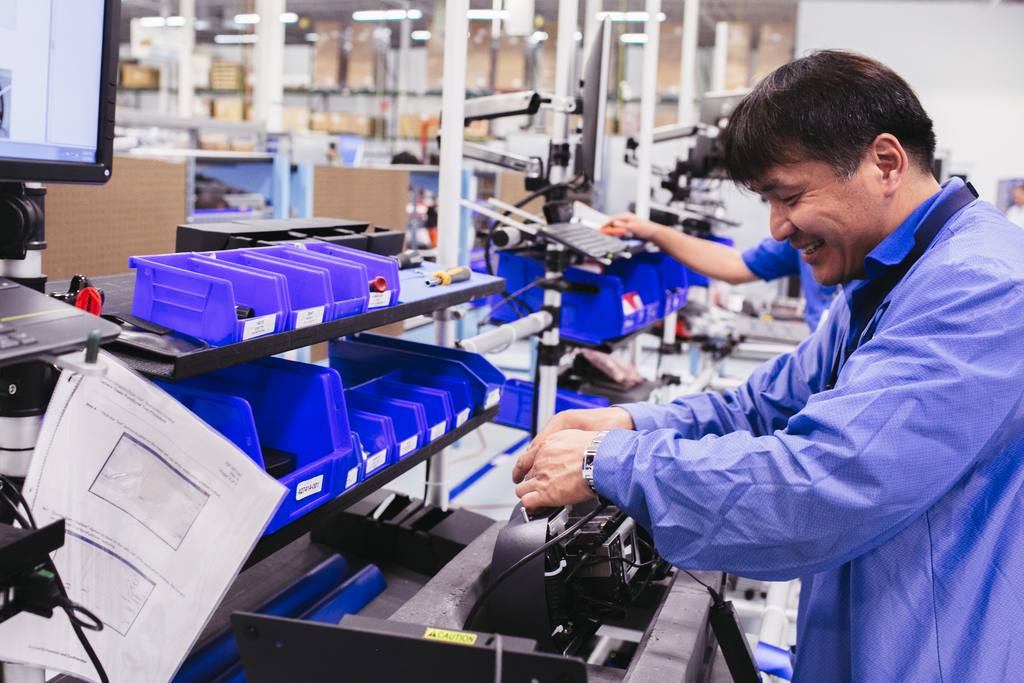
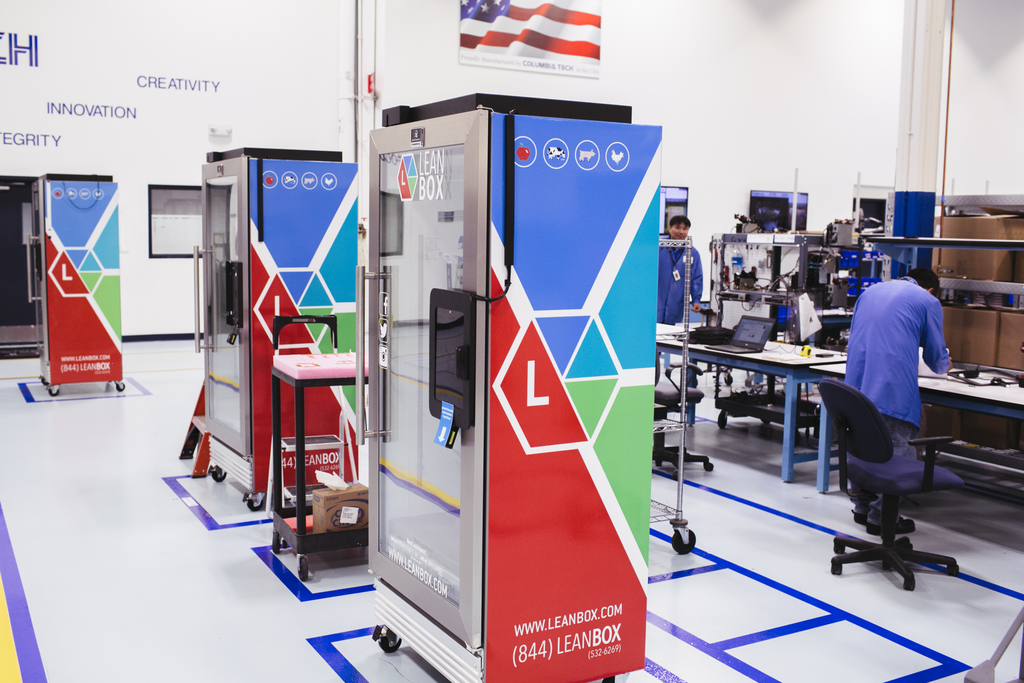
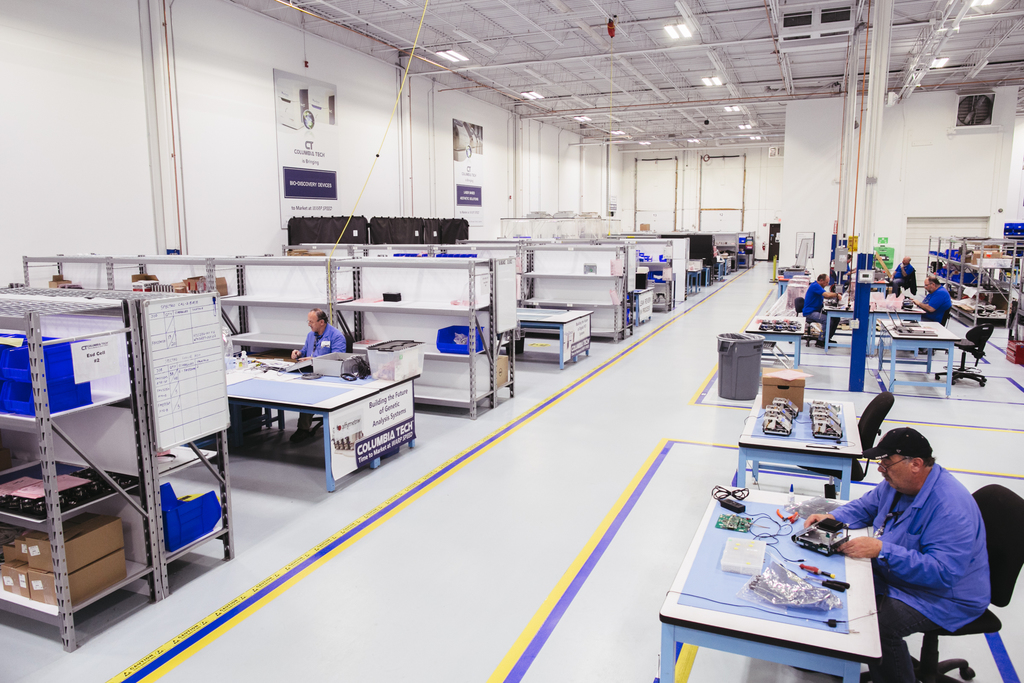